Overview
As the COVID-19 pandemic drives increased focus on occupant health and wellness, the commercial building industry (largely including commercial office and multifamily buildings) is increasingly re-evaluating building operations, with specific attention to indoor environmental quality, maintenance, and cleaning strategies.
The focus on health and wellness in buildings, however, is not new: several rating systems including LEED, WELL Building Standard, Fitwel Standard, and RESET Standard, emphasize the importance of occupant health and wellness in both commercial and residential buildings. Building owners have found that their commitment to certifying under these rating systems can help increase productivity, cognitive function, and occupant satisfaction rates, and now provide greater comfort or ease for occupants returning to an office or spending more time in their residences.
In Washington, DC, health and wellness considerations also need to take into account the District’s environmental goals and building regulations and codes. As the building stock in the District is the largest contributor to greenhouse gas emissions (71%), it is imperative that buildings improve their performance to meet these city-wide goals, which will also to help to meet the growing demand for healthy spaces.
Careful and intentional design, planning, and operations are required to ensure that implementing strategies to address health and wellness have a neutral or minimal impact on energy and water consumption. This resource is focused on viable building retrofits and operational strategies to promote a healthier occupant experience while demonstrating the potential impact they have on energy consumption. In addition, while all conditions are important when considering overall environmental quality of a space, this resource is focused on the impacts of indoor air quality (IAQ).
Strategy analysis & comparison
Intentional design of building improvements and strategies should account for additional energy use, in addition to first costs of equipment and installation. What’s more, strategies for improving IAQ are not mutually exclusive: in most cases a combination of solutions are employed on one building. For example, increased ventilation, enhanced, filtration, and ultraviolet germicidal irradiation (UVGI) can all be implemented on the same air-handling system. Owners of existing buildings should evaluate feasibility, first costs, and energy costs to determine the best combination of strategies for each application. In addition, building owners should engage with the building engineer and a mechanical engineer to evaluate potential strategies and incorporate short-term and long-term solutions.
It is important to note that the cost of these strategies will vary based on the age of the building and energy/water impacts will vary based on associated controls and hours of operation.
Additionally, for specific guidance on establishing an approach, existing building rating system credits can be reviewed for guidance on how to approach the topic:
- LEED BD+C New Construction and LEED O&M Existing Building include IAQ requirements and options within the Indoor Environmental Quality section.
- WELL Building Standard includes an Air Concept category that includes testing requirements to meet air quality levels of particulate matter, organic gases, and inorganic gases; as well as optional features for source control and ventilation, dependent on building typology.
- Fitwel includes optional strategies for developing a building IAQ management policy requires permanently install IAQ sensors in the space, with regular reporting on air quality thresholds
Strategies for consideration
Mechanical system design
In addition to those covered in the rating systems linked above, additional strategies to reduce occupant exposure to harmful aerosols include:
Humidification
Building operators should aim to maintain indoor relative humidity levels between 40%-60% to both reduce the lifespan of organisms and improve occupant health.
Humidification systems most commonly utilize either electric heat or natural gas heating to create mist distribution and are often recommended to have reverse osmosis water filtration, which has operational energy- and water-use increased impacts. It is recommended that sensors be regularly monitored, and systems utilized only during the dry winter season or seasonal abnormalities to reduce these impacts.
There have been various studies on the effect of space humidification on COVID-19. Higher levels of humidity have been recommended to reduce the lifespan of the virus. Since humidity levels above 60% can create occupant discomfort and moisture/mold concerns, exceeding this limit is not recommended. In commercial buildings, these humidity levels are often addressed by the building’s cooling systems in the summer. However, most commercial buildings do not provide humidification in the winter, which can lead to the building’s humidity levels dropping down below this range. Consider adding a humidification system (comprised of a steam generator, piping, and manifold in the ductwork) or portable humidifiers.
Reviewing air-distribution patterns
In addition to ensuring that excess CO2 from human respiration is replaced with fresh outdoor air, use pressurization to create clean-to-dirty flow patterns that allow other airborne particles or aerosols to be captured or exhausted. This can utilize strategies such as underfloor air distribution or displacement ventilation. Grill, register, and diffuser selection will need to be designed for the specific height, area, and use of a space to ensure that the airflow patterns circulate properly.
Differential room pressurization
The pressurization between rooms can be controlled such that rooms with potential higher exposure to contaminants can be isolated or placed under negative pressure. For existing buildings, this would be a major renovation of the existing HVAC design and may require additional units.
Exhaust fans
Typical HVAC systems have dampers to ensure that air is exhausted from the overall system. Specific building locations with known higher levels of contaminants should also have dedicated exhaust fans to remove particulate matter and aerosols from locations such as restrooms or areas where chemicals are used or stored
Mechanical system controls and monitoring strategies
Management and understanding of indoor conditions has never been more prevalent for building operators. Strategies for this include:
HVAC-control strategies |
|
IAQ sampling and monitoring strategies
|
|
Cost and energy impacts
Humidification has the largest overall cost and energy impact of all the strategies. Costs to implement and operate will increase from existing operations if a system needs to be retroactively added.
Air distribution first will require engineering studies and computational fluid dynamic modeling exercises to evaluate existing spaces. Professional engineer consultants should then be able to provide solutions that minimize energy consumption impacts during operations.
Demand control ventilation is a widely referenced energy savings measure to account for conditioning spaces only as needed in areas with irregular schedules. Some buildings can see over 30% savings in energy consumption from these retrofits.
IAQ Sampling will have first costs for either new equipment or services. The annual energy consumption will depend on response and protocols taken in response to the testing results. Operational changes in response to testing should include monthly review of energy usage impacts.
A professional design engineer should be consulted for the strategies in this section. Modeling and calculations of the existing conditions will outline the best solutions specific to each building, as one solution will not fit a building typology.
LEED and WELL do not have requirements for any of these solutions but have optional strategies that will contribute to a building rating system certification if that is also a factor for decision making.
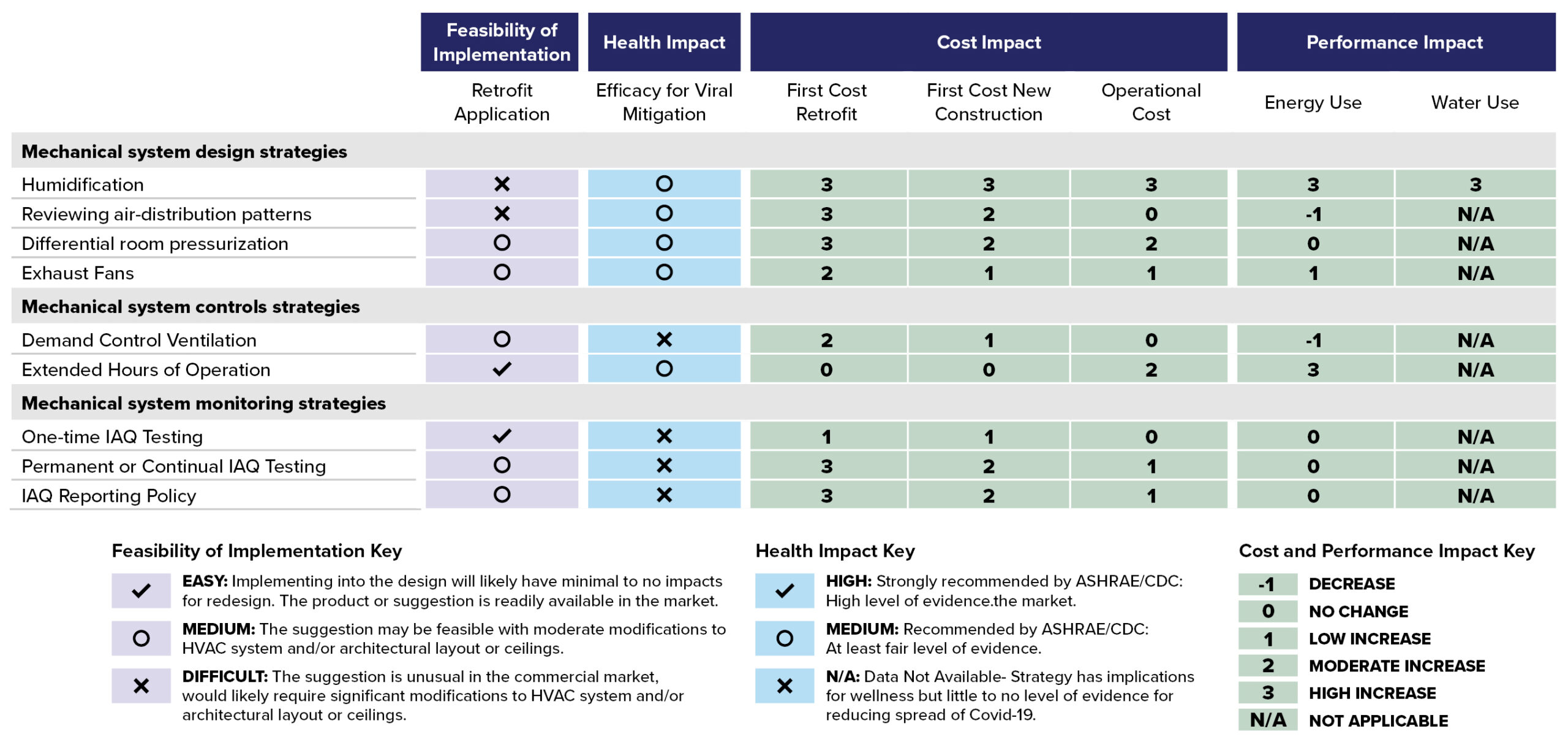
Increased ventilation
Increasing the amount of outdoor air being supplied to a building or space reduces the concentration of pathogens by bringing in clean air and removing contaminants. LEED has set the standard in the U.S. for increased ventilation, typically referenced as 30% above code-required levels.
The following steps should be taken to understand if changes to ventilation systems are appropriate or possible for your building.
- Optimize natural ventilation. If a building has natural ventilation, is it managed by building management and if so, how is it managed? Both occupants and utility bills may benefit from automated cueing from green lights or web-based notices on when the outdoor conditions are optimal for opening.
- Assess existing HVAC systems. Assess air handlers, duct sizes, and current operation to determine if the amount of outside air can be increased, and if this additional cooling and heating load can be provided by the air handlers.
- Talk to tenants to re-evaluate acceptable comfort levels. Consider talking with tenants to expand setpoints (i.e. decreasing winter heating setpoints from 70 degrees to 68 degrees and increasing summer setpoints from 74 degrees to 76 degrees) in order to provide additional outside air to the building without increasing energy demands.
- Consider extending HVAC hours of operation. For improved air quality, consider extending HVAC system hours to ventilate and exhaust before and after occupied building hours. Again, this will increase overall energy consumption, however, can be easily employed on existing buildings without replacing any equipment or infrastructure.
- Increase ventilation rates. If mechanical systems are able to increase ventilation rates based on their rated manufacturer capacity, the highest threshold would be greater than 30% above code in all spaces, as referenced in LEED rating system standards. If system capacity in all locations cannot meet the 30% threshold, additional increases above code could be targeted in most commonly occupied spaces.
Cost and energy impacts
Bringing in additional outside air to increase ventilation rates does not always require it to be conditioned. Additionally, energy recovery and airside economizers can be incorporated to minimize the associated increase in annual energy use. An EPA study found that increasing a building’s ventilation fourfold in Washington, DC increased energy costs of a variable air volume (VAV) HVAC system by up to 5% for low- to medium-occupancy spaces. The energy impact for increasing the outside air in high-occupancy spaces was noticeably greater.
LEED and WELL requirements both reference ASHRAE ventilation standards that must be applied as applicable to the building typology. Additional options beyond minimum requirement are available as optional points to further contribute to certification.
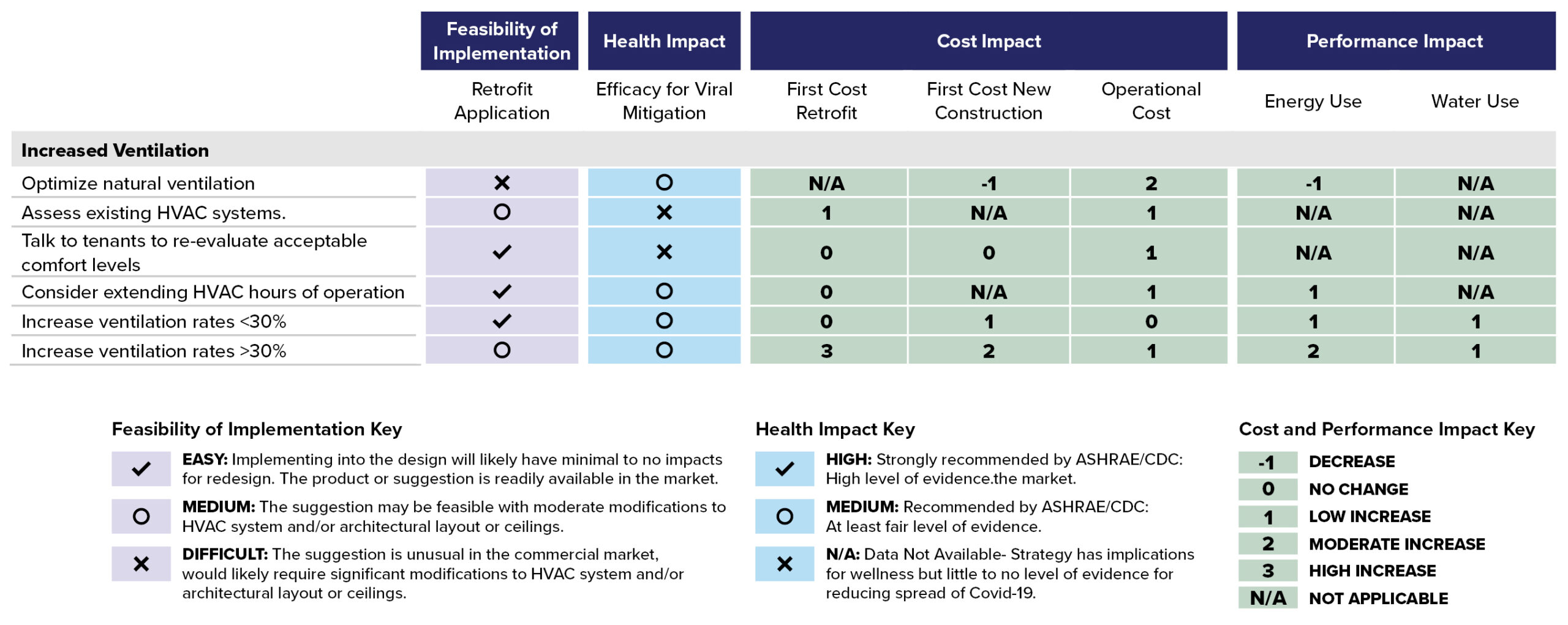
Enhanced filtration
The most common and simple way to remove pathogens or other indoor pollutants is through high-efficiency filtration within the mechanical system. There are two main types of air filters.
Mechanical air filters are commonly used in buildings throughout the District. Air-handling units within the building use these filters to capture particles at a specific size based on the filter level, and can easily be replaced or cleaned on a set schedule. Electronic filters are connected air-cleaning devices that are designed to remove particles from airstreams by electrically charging the particles. These filters are newer to the industry with less research available as to long-term effectiveness.
ASHRAE measures the effectiveness of a filter and assigns it a Minimum Efficiency Reporting Value (MERV). A higher MERV rating demonstrates a better ability to capture smallest particulates. Current building codes in the District mandate filtration for mechanical systems, but not a specific MERV rating. Existing buildings will commonly be using MERV 7 or 8 filters, and new construction may have MERV 13 in line with LEED Enhanced Filtration credit requirements.
Activated carbon filters are an additional strategy that can be utilized when the building is targeting removal of volatile organic compounds and ozone from the indoor air. These filters can significantly increase air pressure drop which affects ventilation rates, and must be evaluated against existing HVAC system capacity before implementing.
Current research related to the COVID-19 pandemic indicates that improving filtration from a MERV-7 (or lower) to a MERV-13 significantly reduces the risk of airborne transmission of viruses including COVID-19.
Strategies for enhanced filtration include:
- Upgrade filters to the highest level achievable. Higher MERV ratings typically imply greater pressure drops throughout an HVAC system. Evaluate the capacity of all air-handling devices to determine if they can handle this additional pressure drop. This pressure drop will increase overall fan energy, which is why employing filters with ratings higher than MERV-13 may not necessarily be recommended.
- Re-evaluate your building’s filter maintenance strategy. Higher-efficiency filters will need to be replaced or cleaned more often. Replacing filters more often will also save fan energy by reducing the pressure drop through dirty filters. Ensure that filters are at least being replaced or cleaned on a seasonal basis, and consider more frequent replacement if there is a higher risk of dust or other airborne particles.
Energy impacts
Research studies have shown that that increasing the level of filtration has a small increase on energy consumption. Additional research in the industry is necessary to determine the impact of improving filtration on small terminal units without decreasing airflow.
To implement changes in filtration, the flow chart below outlines the sequence of evaluation to ensure it will not negatively affect overall mechanical system operation. Additional benefits for any rating system certification contributions should remain secondary, as ensuring that all systems are fully operational should be priority.
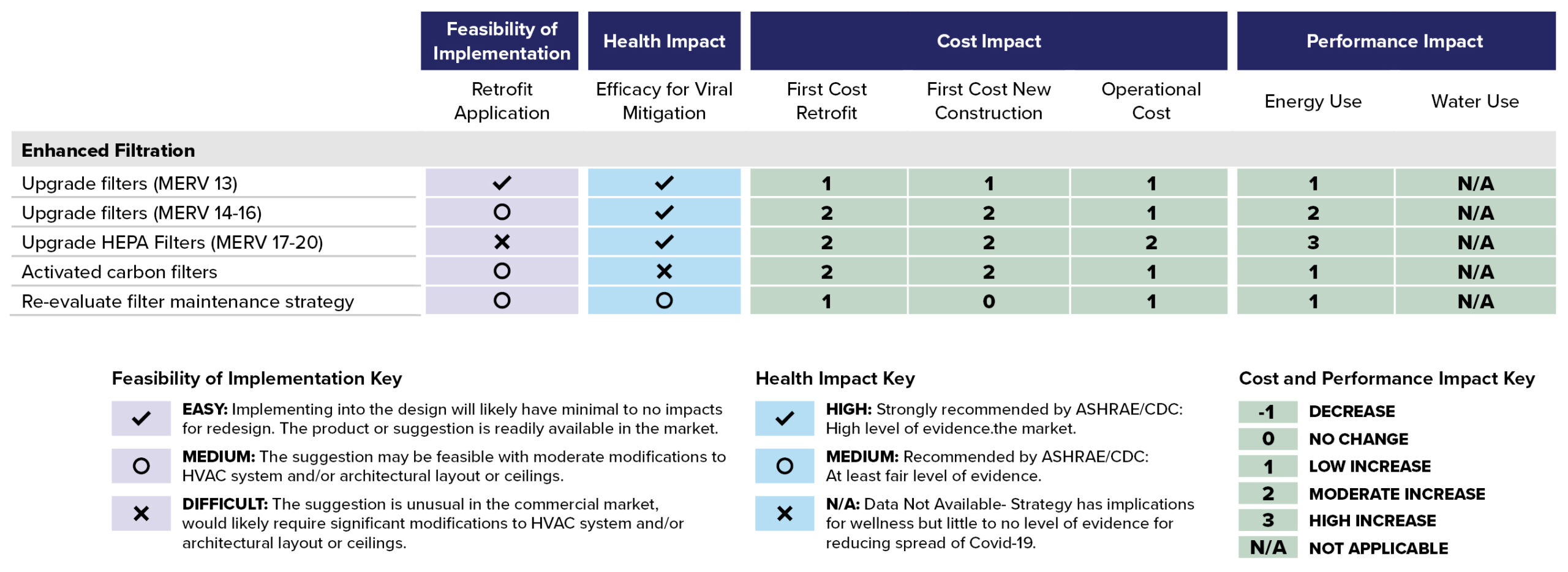
Air cleaning or purification
Air purification refers to the process of removing contaminants or particles from the air. Common strategies include:
- Bi-polar ionization, a process using opposite poles to split, and thus clean, atoms in the air
- Sorbent-based air cleaners, a physical and chemical process to remove gaseous contaminants from the air
- Photocatalytic oxidation (PCO), which utilizes photons from an ultraviolet light shining on a catalyst to create ionic reactions to decontaminate air or surfaces
- Ozone-generating air-cleaning devices that use electricity during air cleaning have the potential to generate ozone, which must be managed in relation to human health
- Packaged air cleaners using multiple technologies , i.e. UVGI and/or filters
Take the following steps to understand if air purification strategies are the appropriate strategy for your building:
- Evaluate and carefully study health impacts for each option. Many electronic air cleaners emit significant ozone, which can lead to negative health effects. Exposure to ozone is to be minimized by implementing these technologies only on unoccupied rooms and leaving rooms unoccupied for a certain amount of time.
- Understand the limitations and proper applications for air purification technologies. Many air cleaning technologies are new to the market and do not have available data indicating long-term effectiveness.
Cost and energy impacts
Air purification systems at a commercial scale (for both multifamily and office buildings) are newer to the market as compared to residential portable systems. All system options for air purification will have first costs and increased energy consumption dependent on operating run times. Operational plans and policies for these systems will help manage the long-term energy increases as compared to occupant benefits.
Air purification systems are often one of the last options evaluated due to the highest costs and energy impacts. Professional engineers can help building owners vet viability of systems, and manufacturer testing information for the efficacy of a specific building.
Rating systems do not yet address air purification system, but custom solutions that solve a specific operational problem could be submitted as innovation credits.
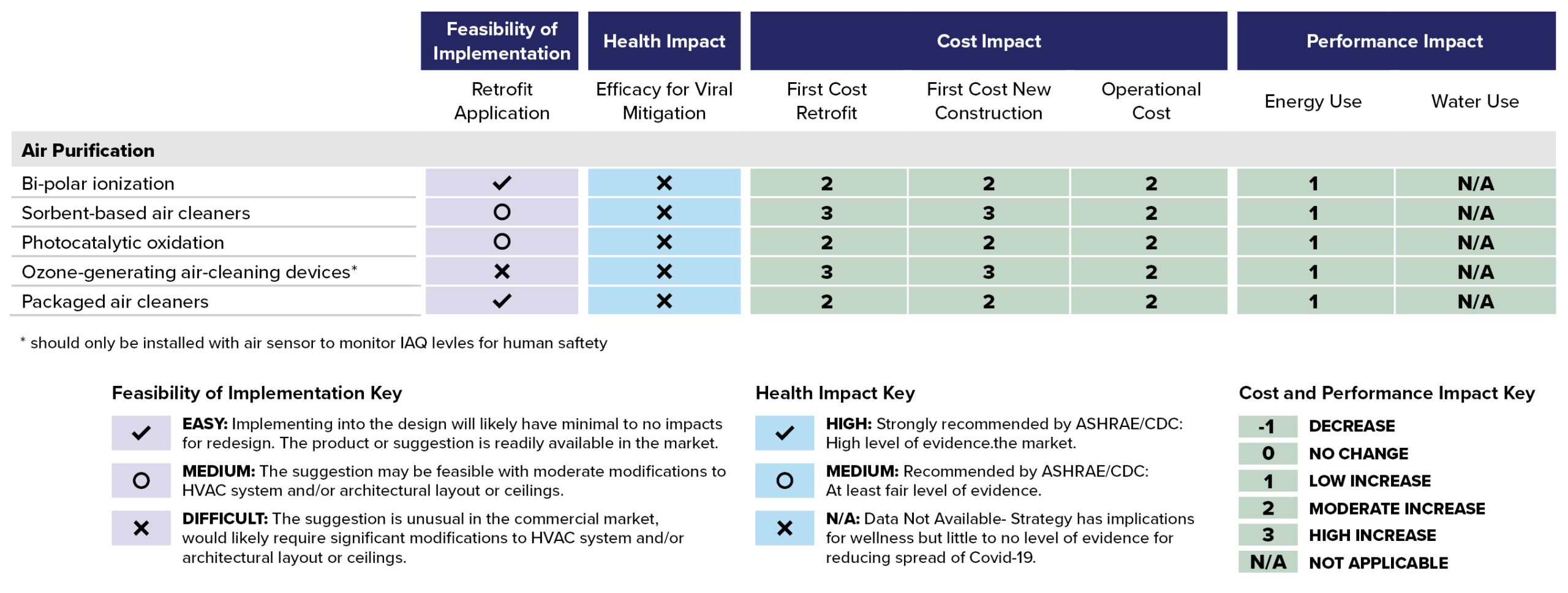
Ultraviolet germicidal irradiation
Ultraviolet germicidal irradiation (UVGI) utilizes UV-C light, which is strong enough to destroy genetic material used for pathogen control, air sanitation, and/or HVAC coil cleaning. It has long been used in the healthcare industry with well-documented evidence for its effectiveness to reduce pathogen transmission, but is not yet commonly found in the commercial office or multifamily DC market.
UVGI lights can be portable or be permanently installed within a specific room or the HVAC system. Portable UVGI systems are traditionally used in healthcare facilities, and have robotic operations that can safely be used in space-by-space applications. For more permanent applications, UVGI can be effectively implemented within the mechanical unit coils directly in the air ducts. It is most common to install at the central unit either upstream or downstream of coils, dependent on physical space availability. Duct applications can also be used to treat air before being recirculated into the space.
Exposure to UVGI rays during use are dangerous to humans, and lamp disposal should be managed with proper hazardous material protocols due to mercury. In-room lights should only be operated during unoccupied hours, and use extreme caution when installing lights in HVAC system.
Cost and energy impacts
UVGI retrofits in existing buildings are typically feasible and have a short construction timeline. UVGI HVAC applications can often be costed based on the cubic feet per minute system capacity. Portable units require safe, secure storage locations within the building. Studies show that UVGI has a minimal impact on energy performance. A simulation study found that adding UVGI had a minimal (0.3%) increase to a building’s energy consumption, or less than half of the energy associated with improving HVAC filtration to achieve the same health benefits.
UVGI applications must evaluate available space within the HVAC system or for proper storage of portable systems first, followed by developing an outline of how often the systems will be utilized. Based on these priority factors, operations and building owners must be involved to ensure a safe policy is developed for use.
The WELL Building standard has an optional strategy for implementing UVGI systems which is aimed at mitigating mold and microbe growth in the HVAC system which can contribute to certifications.
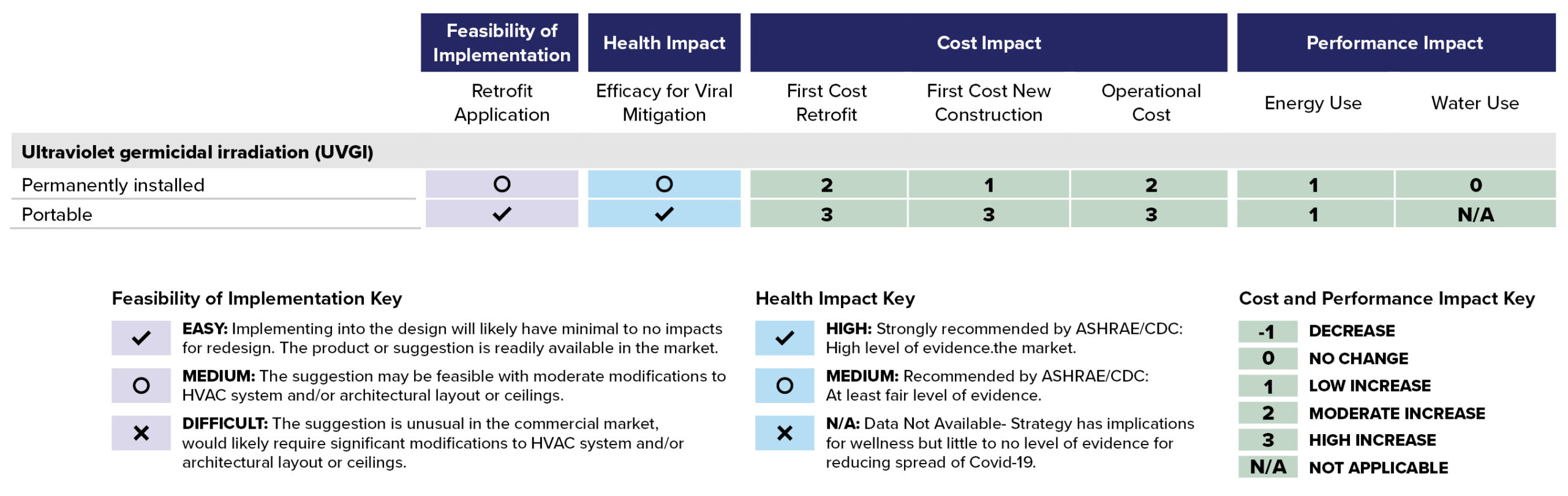
Smart building technology
Smart building technology in commercial buildings can enhance building monitoring and assessment to provide cleaner and healthier environments, as well as increase the level of transparency available to the occupants. It can monitor things like occupancy, air quality, lighting, energy consumption, and even real time occupant feedback.
It identifies problems with building systems via sensors placed throughout the building. This results in more-efficient building management and maintenance. Smart buildings can help optimize building operations to balance indoor air quality and reduced energy costs by providing real time or interval data. This can be important if the facilities and operations managers are not responsible for utility bills, and may not receive the monthly energy or water usage data. Strategies include:
- Touchless technology. New solutions that integrate a touchless building system paired with an internet-connected personal device are readily available in the market, and currently being deployed for use in shared elevator systems and HVAC controls to avoid touching a communal surface.
- Smart building software applications. Software systems for the building management system or building automation system can develop custom solutions based on the occupancy, schedule, and use of each building. They can program daily, weekly, or one-time automation into items controlled by the central system.
- Daylighting controls. Smart building systems can control LED light fixtures on both a schedule, as well as use photocell sensors to know when proper levels of daylight are illuminating interior spaces. Increased daylight can contribute to optimal human health and help the body naturally regulate circadian rhythms, which research has shown can help with healthy sleep patterns that in turn increase focus and productivity.
Cost and energy impacts
Smart building applications shift costs from day-to-day operations and maintenance staff to procurement of the new technology applications. When properly commissioned and programmed, they are intended to have minimal operational staff labor requirements and reduce annual energy and water consumption.
Smart building applications are typically only limited by the software platform and availability of internet connectivity (either wireless or hard wired). This allows for existing buildings to scale up based on current capacity, or upgrade at the end of a determined lifecycle.
A rating system specific to smart buildings, WiredScore, evaluates the digital infrastructure of the building.
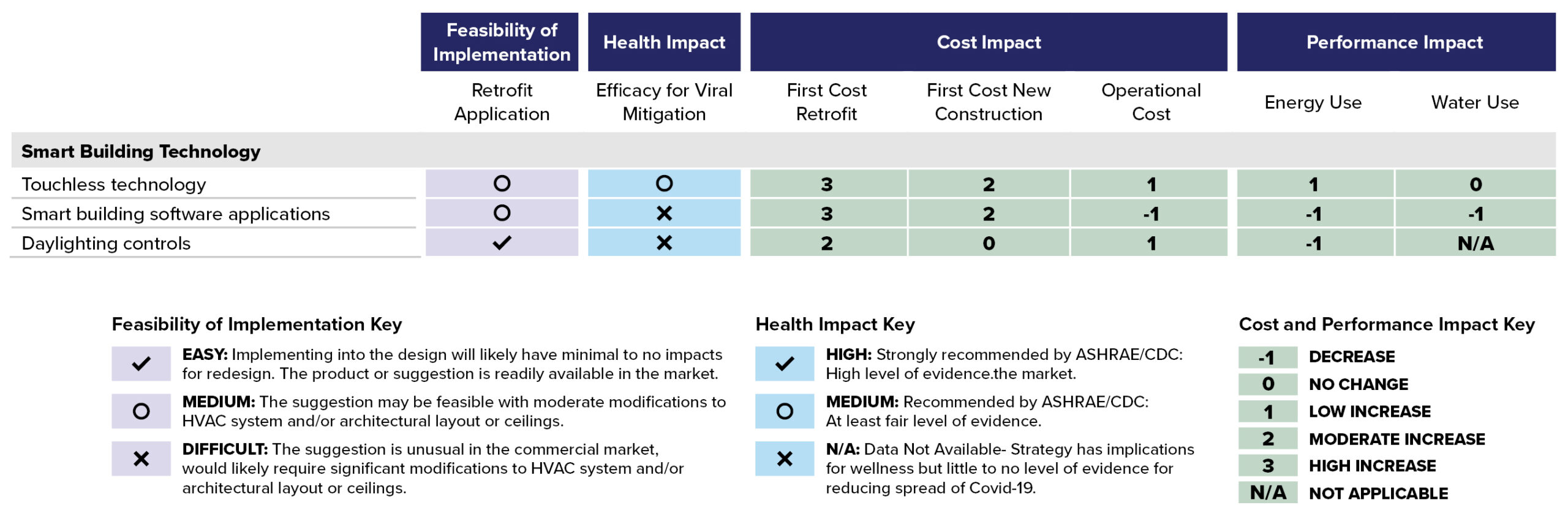
Building policies and occupant participation
Numerous policies and protocols can be put into place to impact health and wellness with no impact on energy consumption. Strategies include:
- Cleaning policies. Ensure cleaning strategies are implemented, especially for high-occupancy spaces. The EPA has established cleaning protocols for disinfecting surfaces. Specific attention to cleaning high-touch surfaces should be made, and automation options to reduce contact should be considered. COVID-19 pandemic impact: Specific disinfecting practices can be found at both the CDC and EPA websites. Building owners should also focus on general upkeep while their building is unoccupied.
- Pest management policies. In conjunction with the cleaning policies, it is best practice to also include prevention protocols for pests on both the interior and exterior areas of the building.
- Entryway pollution prevention. Walk-off mats can be either permanently installed or non-permanent and maintained by a regular cleaning service company. It is recommended that walk-off mats be at least 12 feet long in the direction of entry travel to capture 90% of outdoor contaminants.
- Waterborne safety. Before reopening after a renovation or construction, buildings should be canvassed for issues such as mold and legionella prevention that can be developed during the unoccupied months.
- Handwashing. Add signage to encourage frequent handwashing and ensure adequate supply of antibacterial hand soap.
- Occupant survey. Feedback from occupants of the building can be extremely important to evaluate the effectiveness of solutions that are implemented in the building. Best practices should include a policy for responding to this feedback where measures are not having the intended impact. The energy and water impacts associated with this strategy will vary based on survey results, but should be included in the response policy for management.
Cost and energy impacts
Building owners must ensure that proper follow-through for any plans or policies can be executed with the necessary level of staffing. Operational policies and plans can be developed internally if there are appropriate staffing allocations, or outside specialists can be hired to develop and implement. All policies should include energy- and water-use best practices to reduce unnecessary utility usage with any changes.
LEED includes many of these best practices as optional credits, or as an opportunity for innovation credits.
WELL pioneered the legionella management and handwashing credit in their rating system and has seen significant traction with manufacturers to implement these standards for optimal health and hygiene.
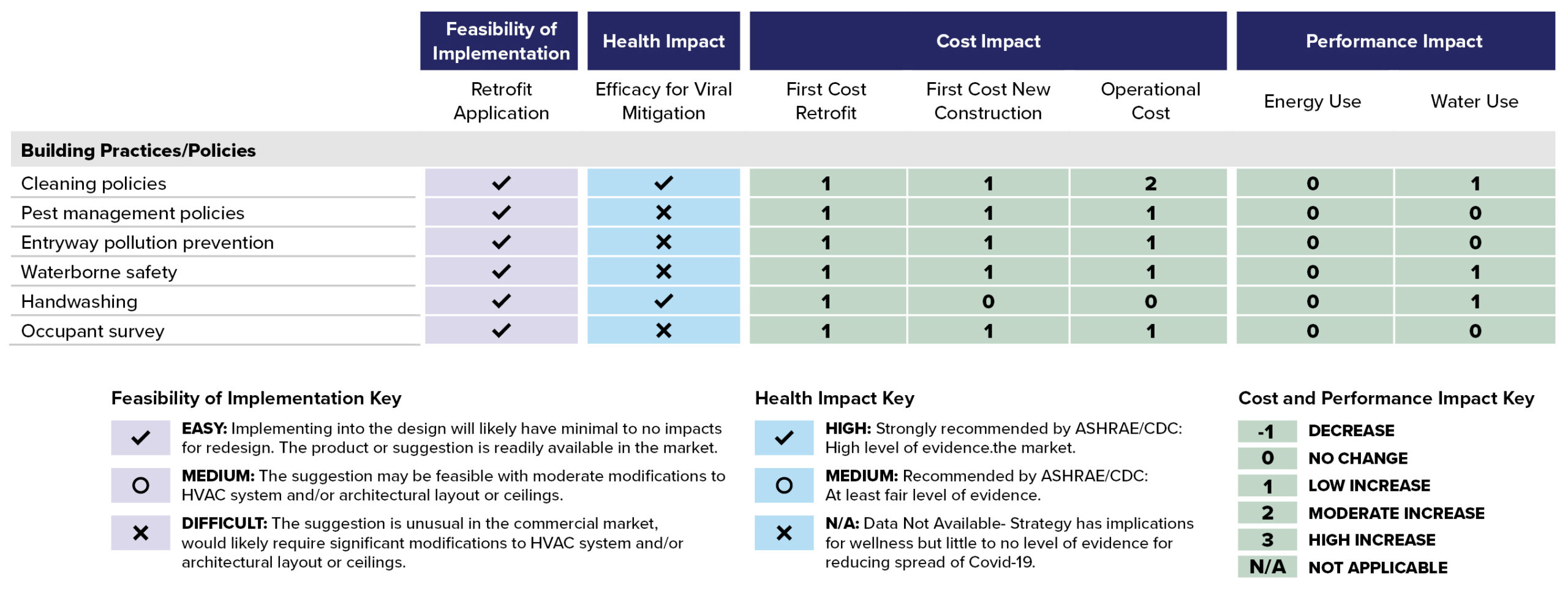
Summary technical resources
Many of the recommendations for system solutions contained here are based on guidelines from ASHRAE and the Federation of European Heating, Ventilation and Air Conditioning Associations (REHVA), as noted below.
ASHRAE | Indoor Air Quality | Standards 62.1, 62.2, and 189.1 |
ASHRAE | Indoor Air filtration | Standard 52.2 |
ASHRAE | Indoor Air ventilation | Standard 62.1 |
REHVA | Airborne Infectious Diseases | REHVA COVID-19 Guidance |
ASHRAE | Risk Management of Public Health and Safety in Buildings | Guideline 29-2019 |
ASHRAE | UV Air and Surface Treatment | 2019 Applications Chapter 62 |
ASHRAE | Epidemic Task Force | Building Readiness 2020 |